Certificates
Process
There is supervision and reporting at every stage. For instance:
Entirely new product category–
A prototype after being made is subjected to not only Hydrostatic test and operation but “Proof of design test (POD)”. In POD the valve seat is made to open/close under hydraulic pressure certain number of times (2000 to 10,000 depending upon size) without any sign of leakage or pressure drop and at the end of the operating cycles, it is stripped down to assess wear and tear. The tests are often witnessed by competent inspection agencies like Bureau Veritas. The largest valve having undergone such POD test was a 2400 mm dia butterfly valve.
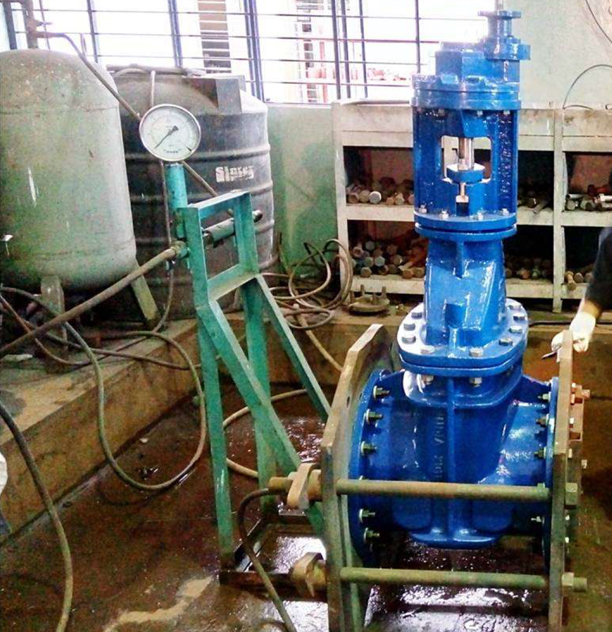
POD TEST
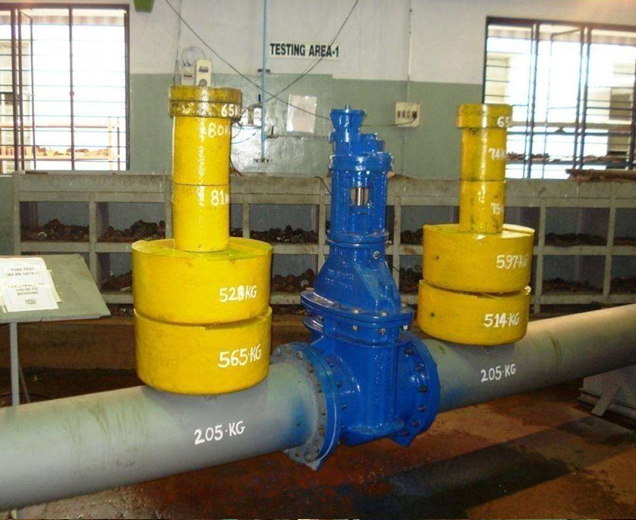
TYPE TEST – RESISTANCE TO BENDING
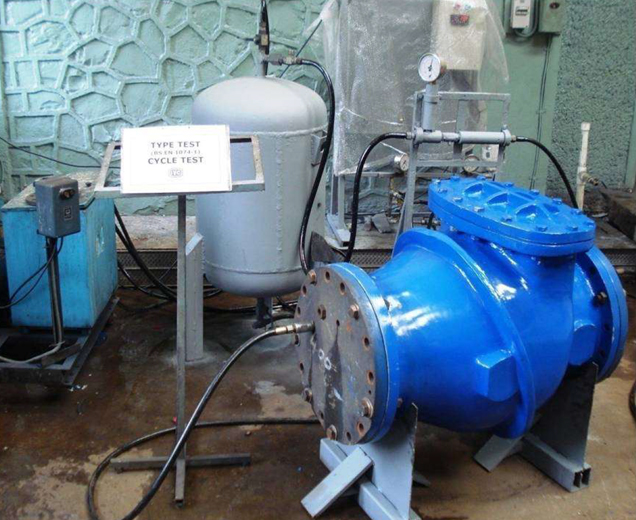
TYPE TEST – CYCLE TEST (DOOR OPERATION)
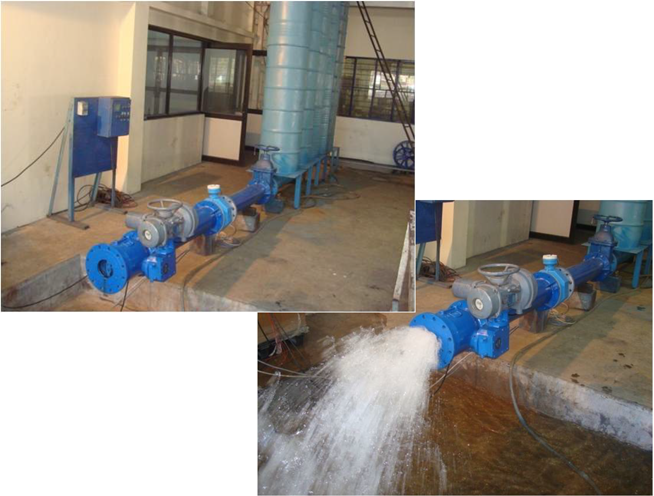
Likewise, the first 200 mm diaFlow Control Plunger Valve was tested hydro dynamically, in house, using a setup involving a flow meter, a PLC based hardware to set / change parameters, a modulating duty electric actuator, large overhead water storage and piping.
Bulk of our valves today are in DI construction. Each and every melt before a casting is poured at the foundry level, the metallurgy is checked using Spectro meter; all large castings come with integral test bars to independently check nodularity and physical properties.
Billets and raw shafting are procured from vendors of repute, ultrasonically tested for internal flaws, physical and chemical properties checked in NABL approved labs before these are accepted for processing.
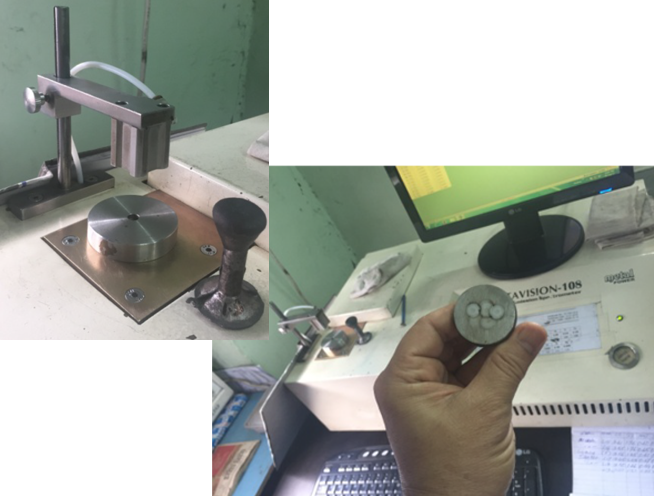
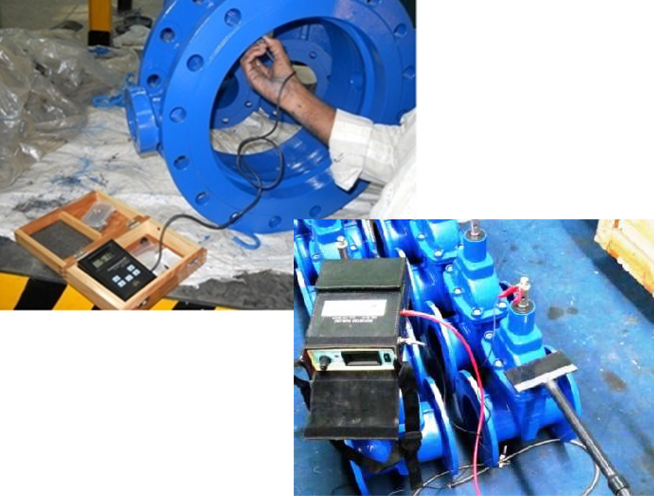
Paints and rubber components are procured from WRAS certified vendors. Coating / painting, be it electrostatic powder or liquid epoxy, is subjected to usual tests like dry film thickness, adhesion, holiday free and scratch proof. Prototypes have been tested at the National Test House at Kolkata and certificate obtained.
All gauges and metering devices are routinely tested at an independent NABL lab and upto date certificates kept.
All valves, regardless of size, are Hydro tested as per relevant standards, 100% before they are passed and qualified for supply.
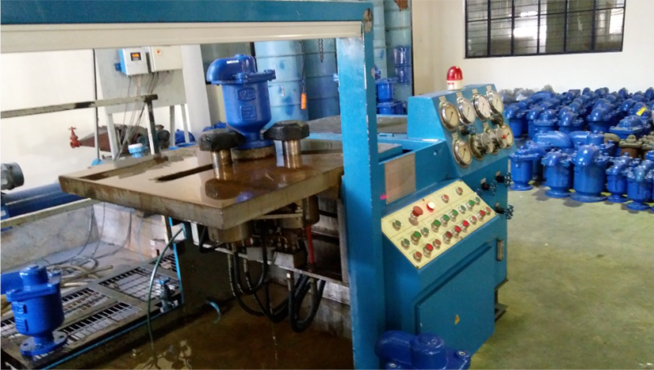
In most cases, a large batch of valves when ready, are subjected to thorough inspection and testing by reputed inspection agencies like:
- Bureau Veritas
- SGS
- DNV
- Certification Engineers International Ltd.
- RITES Ltd.
- TATA Projects Ltd.
and several others.
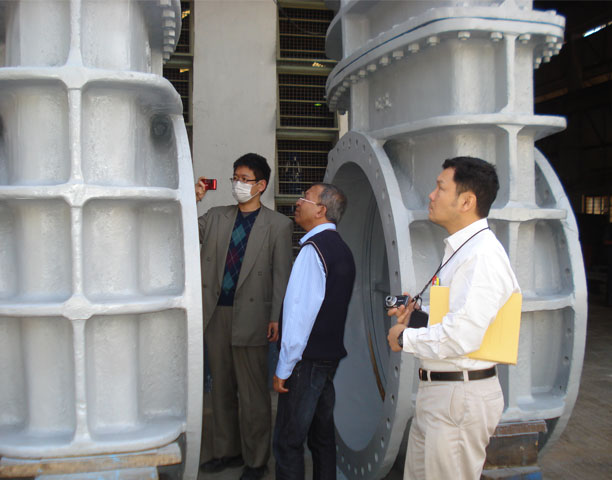
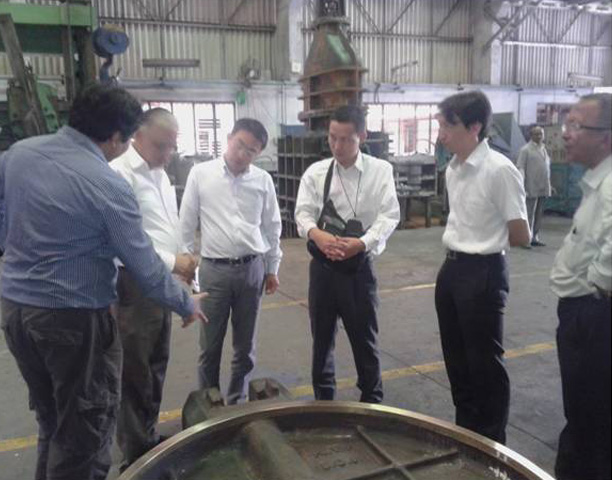
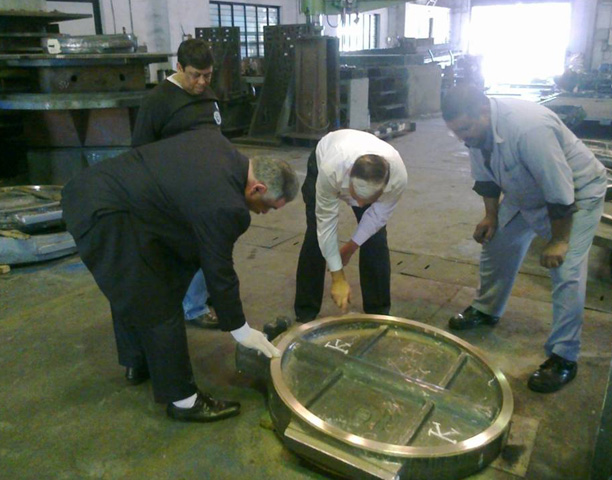
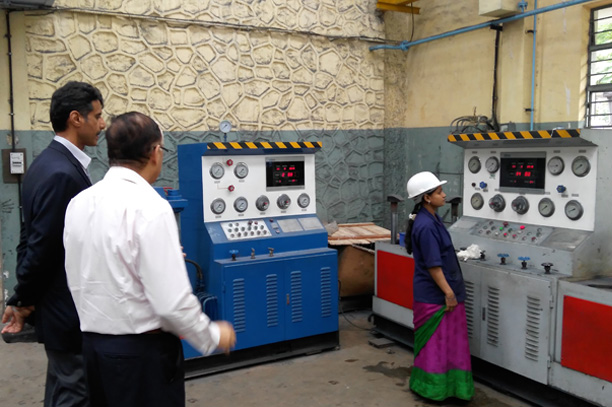
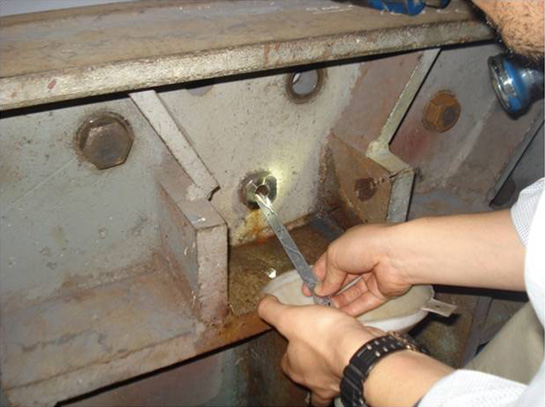
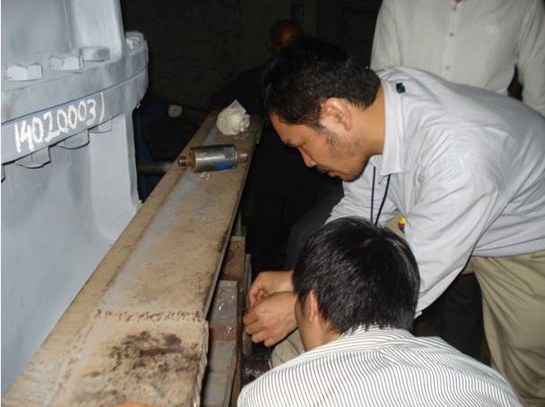
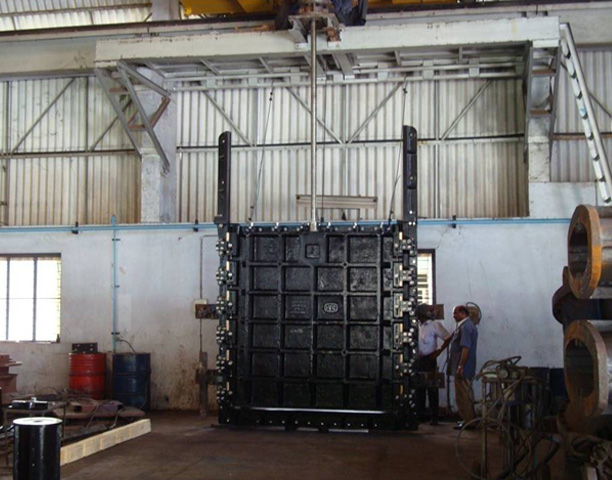
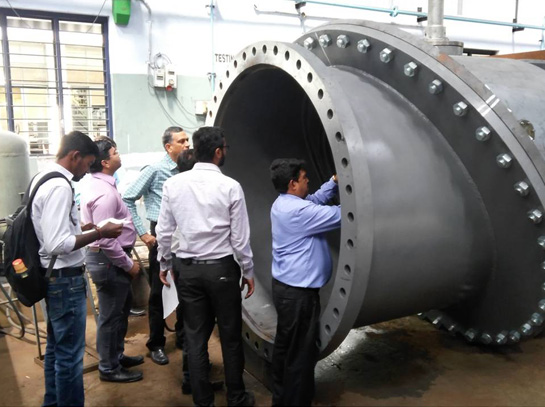
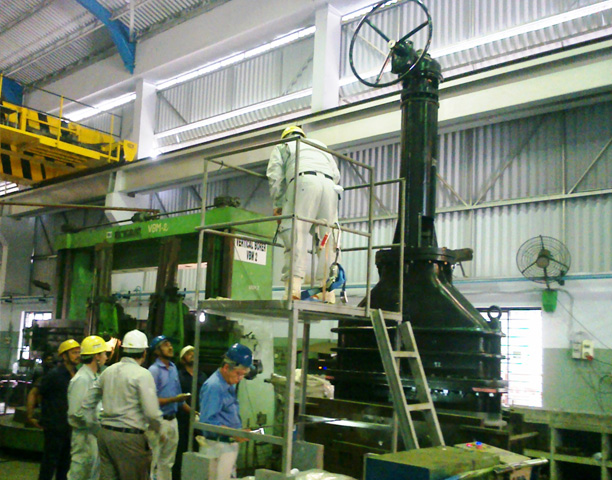
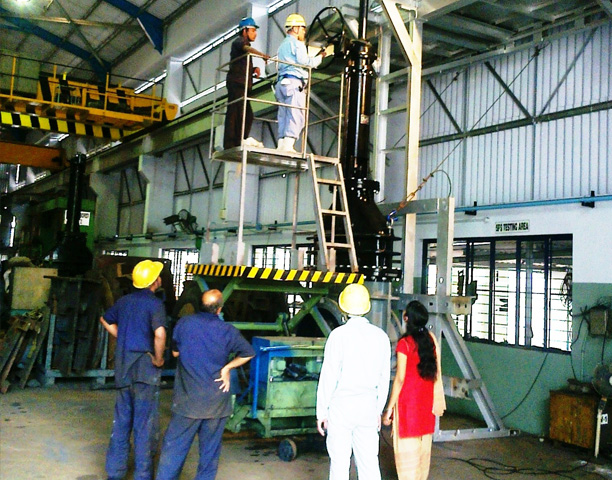

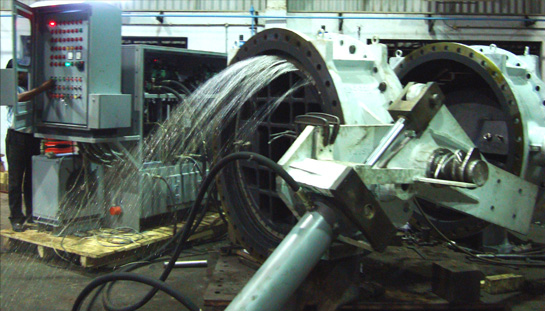
It is our endeavour to see that each valve that leaves our factory renders satisfactory service for 2-3 decades for “valves built to last” is what “IVC” stands for.

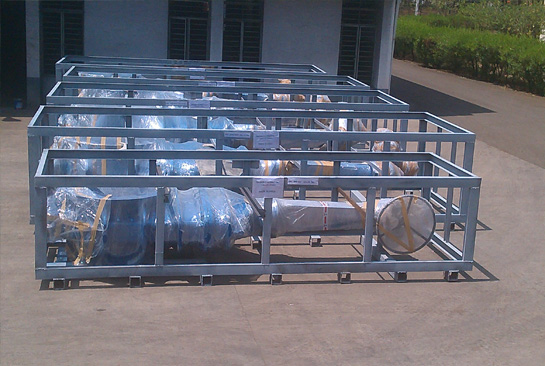
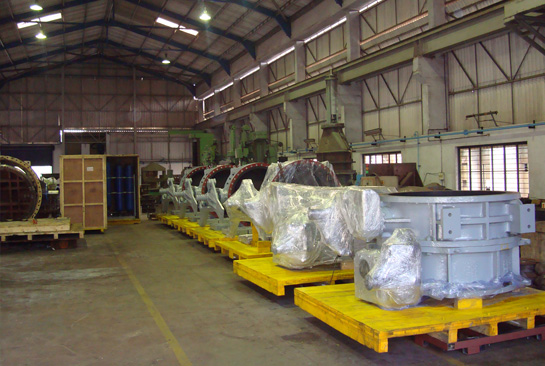
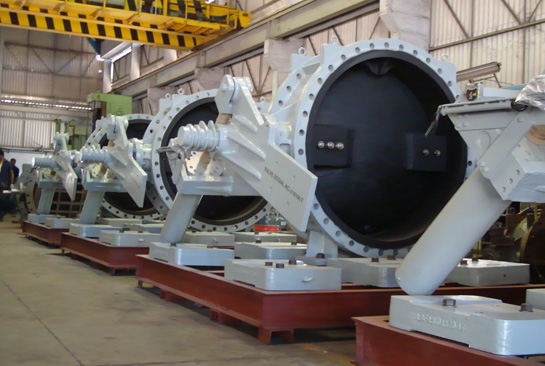
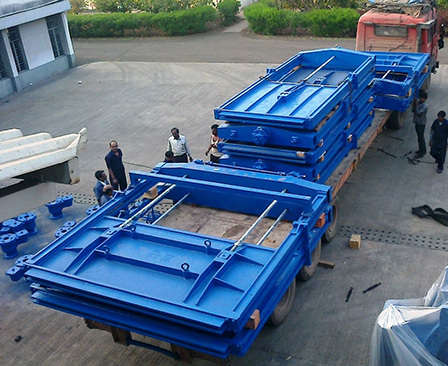
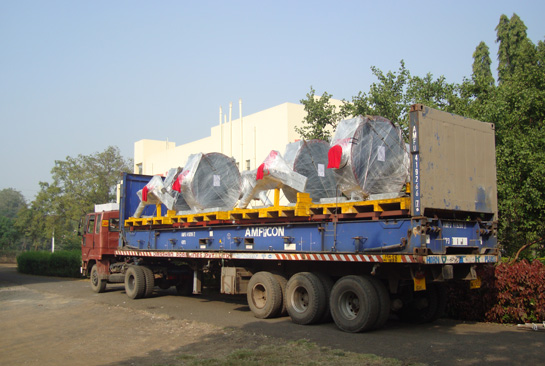
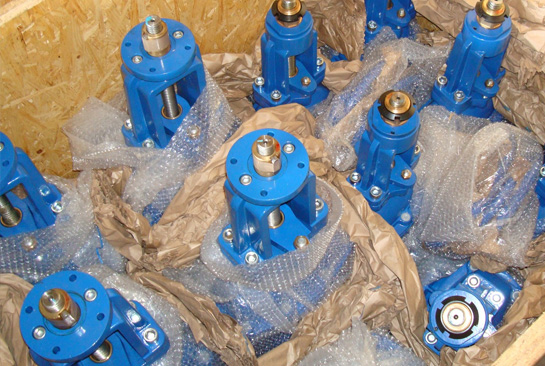
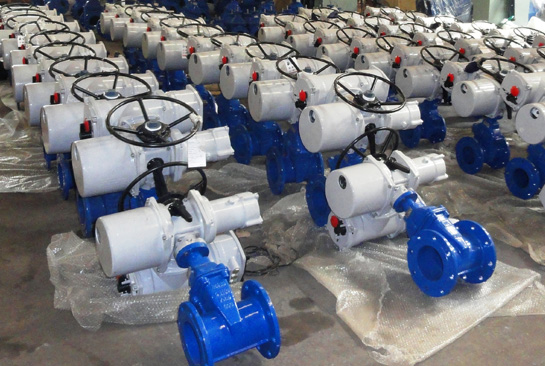